Freshwater generators are the kind of equipment installed onboard, that produces distilled water mainly for the ship’s consumption, whether it is for the main and auxiliary engines or for the crew’s usage. The abundance of seawater surrounding the ship is converted to distilled water onboard by applying heat to the water inside a vacuumed chamber which will boil at around 40-50oC and evaporates.
The evaporated water will be condensed thus producing distilled water in the process. Some ships, take sufficient potable water on board to fill the requirements needed for the crew and its passengers but this will be unsatisfactory for the use of boiler waters and cooling water for the engines.
Water is a fundamental key to surviving, working, maintaining the temperatures of the machinery, and keeping the cleanliness onboard. Generally, the average consumption of water onboard is around one to three tons per day. It is used mostly in cooking, lavatories, laundries, boiler consumption (for steamships), personal use, etc.
As we continue this article, we will learn about the types, working principles, and components of freshwater generators onboard.
Working Principle Of Fresh Water Generator
The basic principle of a freshwater generator is about reducing the boiling point of water by introducing it to a vacuumed condition chamber. By this, water can boil at a low temperature approximately about 40-60oC. Moreover, the water is heated by utilizing the waste heat coming from the jacket cooling water of the main engine or by the use of steam.
A combined air/brine ejector creates a vacuum inside the evaporator chamber by continuously driving the seawater through the ejector, passing it through the condenser before it is discharged overboard. As the seawater passes through the ejector, the air/brine, as well as some seawater inside the evaporator chamber, is suctioned as well, creating a state of vacuum inside the chamber.
In addition, the ejector is driven by an ejector pump. Here is an example of an ejector:
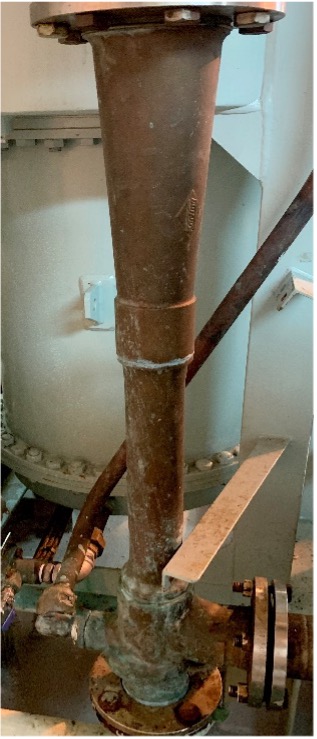
A line from the seawater pipe is connected to feed seawater into the heater/heating chamber. The feed water is controlled by a feed water adjusting valve. We control the feed of seawater in order not to cause flooding inside the evaporator chamber.
Here is a sample diagram of a freshwater generator:
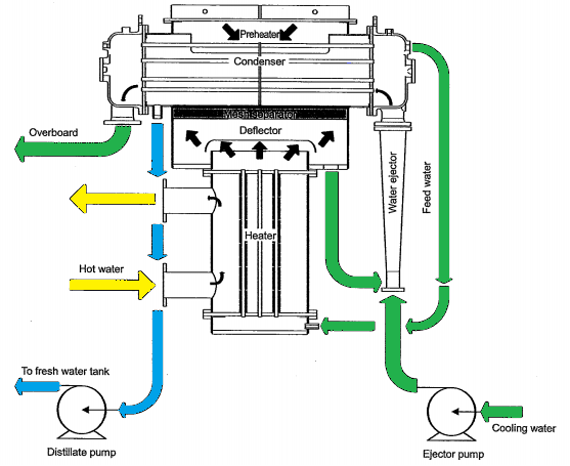
- Green indicates seawater
- Blue indicates distilled water
- Yellow indicates the waste heat of the main engine (jacket cooling water)
The feedwater entering the heater is heated by the waste heat of the main engine which is the jacket cooling water. The seawater will boil and evaporate at around 40-60oC due to the vacuum conditions made by the air/brine ejector. The water spray and droplets are partly removed from the vapor by the use of the deflector mounted on top of the evaporator. The separated water and droplets fall back to the brine and will be extracted again by the ejector.
The vapor that will pass through the demister will be filtered from salt and seawater and will be further condensed into the condenser by means of incoming cold seawater.
The distilled water that is produced will be pumped out by the distillate pump, delivering it to the freshwater tanks. However, the salinity of the distilled water is controlled by a salinometer and a solenoid valve, which opens and returns the water back to the evaporating chamber if the salinity exceeds the maximum limit. This prevents contamination of the made water.
Excess salinity could be caused by factors like the malfunctioning of the demister, flooding inside the evaporator, leaking condenser tubes, worn-out ejectors, and many other reasons.
Gasses or steam that cannot be condensed by the condenser is considered incondensable gasses. Fortunately, these gasses are also ejected continuously by the air/brine ejector. In this manner, the evaporator chamber will be maintained in a vacuumed state that is needed to boil the water below its boiling point.
Types Of Fresh Water Generators On Ships
There are several types of freshwater generators onboard and they are according to their construction. However, whatever their difference is, they still have the same goal, to be able to produce distilled water onboard.
Submerged Tube-type Fresh Water Generator
This type of freshwater generator is using two sets of shell and tube heat exchangers. One is placed on the lower part which acts as the evaporator or heater and the other is mounted at the top which serves as the condenser.
Example of a submerged tube type.
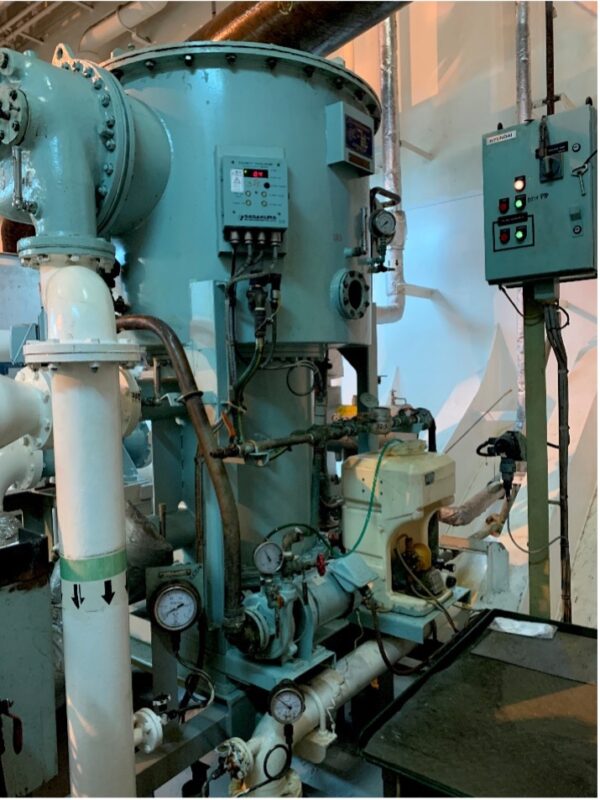
Plate Type Fresh Water Generator
Plate type fresh water generator is almost the same as the submerged tube type, the only difference is that it is using plates as heat exchangers for both evaporators and condensers.
Both this type of freshwater generator has the same principles mentioned above. They both use an ejector to create a vacuum inside the evaporator chamber and suction brine/air, use waste heat of the main engine as a source of heat, and use a distillate pump for pumping out distillate water but is controlled by a salinometer.
Fresh Water Generator Components
The freshwater generator comprises different parts that work together to produce distillate water.
Let’s list all the main components of freshwater generators:
- Evaporator– This a chamber where it evaporates water at a lower temperature
- Vacuum gauge– it indicates the vacuum inside the chamber
- Salinity indicator– indicates the salinity of the distillate water
- Salinity cell– is a sensor for measuring the salinity of the generated water
- Solenoid valve– opens up to return high salinity distillate back to the evaporator
- Condenser– the one responsible for condensing the vapor to create a distillate
- Sight glass– it allows the inside to be viewed
- Distillate pump– discharges distillate water
- Relief valve– protects the inside of the freshwater generator against possible damage and over-pressuring
- Vacuum adjust valve– increases the evaporating temperature during operations in a low-temperature sea area
- Water ejector– maintains vacuum inside the evaporator; discharges brine and air/gasses overboard
- Ejector pump– the pump that feeds the driving water into the water ejector to the freshwater generator
- Bottom blow-down valve– used to blowdown the feedwater from the freshwater generator
- Heater– is the heat exchanger fitted to heat the feed water
- Condenser air outlet valve– releases air from the condenser
- Feed water adjusting valve– controls the rate of the sweater to be fed
- Heater air outlet valve– releases air from the heater
- Vacuum breaker valve– used to break the vacuum inside and restore natural atmospheric pressure
- Integral flowmeter– indicates the total amount of water made
Therefore, we must consider that the freshwater generator is essential onboard. Without it, the supply of water would be deficient which will result in unprecedented outcomes. Extreme care must be done in handling the freshwater generator. Operate the valves gradually. Make sure that the ejector pump inlet is filled with seawater and that the distillate pump never runs dry.
Moreover, before the ship comes close to a port, land, or river, stop the freshwater generator. The seawater in such locations may be contaminated with bacteria and it may be mixed with the generated distillate water.
In the next articles, I will teach you how to start and stop the freshwater generator, as well as adjust and troubleshoot the system.
- Types of Gas Carriers as per IGC Code – April 22, 2025
- Wind-Assisted Propulsion Systems (WAPS): A Game Changer for Maritime Decarbonization – February 6, 2025
- 10 Boat Salvage Yards in California – January 25, 2025