Cargo ships experience a lot of wear and tear during their overseas voyages. Even the largest and strongest vessels aren’t immune to the ocean’s powerful effects. When a ship is damaged, it must undergo an extensive repair and inspection process before getting back to work.
Here’s everything involved in repairing, restoring and redeploying damaged ships in the maritime shipping industry to ensure safety and structural integrity.

Types of Ship Damage
The first step in repairing damaged ships is determining the type of damage. A commercial vessel can experience four types of harm at sea — collision, structural, equipment and environmental.
Collision damage is the most common type. Ships can experience this by running aground or colliding with rocks, reefs, glaciers and other vessels. These accidents largely boil down to human error.
Structural damage is the slow wear and wear that ships experience from saltwater and other corrosive substances over time. Equipment damage is concentrated in a specific location on the boat due to a sudden malfunction or improper maintenance. Environmental damage includes harm from storms, floods and other natural disasters beyond anyone’s control.
In the worst-case scenarios, the damage is so severe that the ships never return to shore. Between 2013 and 2022, 807 vessels were lost at sea, and 338 were cargo or container ships. Repairs and restorations play key roles in preventing these tragedies because many are caused by human error or equipment malfunctions.
Additionally, maritime vessels only have a life cycle of about 20 years before being scrapped for parts. At a certain point, it’s more sensible to put the ship out of commission than to spend thousands on extensive repairs.
Key Steps in the Ship Repair Process
The length of the repair process can widely vary based on the ship’s size and the extent of the damage. For simplicity’s sake, the process can be divided into five main steps — initial assessment, dry docking survey, repairs and replacements, painting and coating, and nondestructive testing. Here’s a detailed breakdown of each step.
Initial Assessment
The first repair step is a thorough assessment of the damage. It’s worth noting that all ships receive an evaluation every 24 to 30 months regardless of their condition. This inspection is required for the boat to maintain its certifications. Employees must also renew their international certificates of competence every five years.
Collision and environmental damage require the most time-sensitive assessments to determine if sinking is a possibility. Crews must take many precautions in cases when the ship is taking on water. They must close watertight doors and hatches, shut all open valves, perform a draught assessment on the hull, and remove as much water as possible before help arrives.
Structural and equipment damage is less urgent than the other two types, but a timely assessment is still required. The crew goes through all the controls and components for equipment damage to identify the problem. For structural damage, they examine the area for leaks and add extra protection with marine epoxy resin if necessary.
After determining the extent of the damage, the ship returns to shore on its own or with a tugboat’s help. Damaged vessels usually return to land as soon as possible to avoid violating the International Convention for the Safety of Life at Sea and other maritime labor laws.
Even if the vessel can complete the voyage, there’s no point in putting the crew in more danger.
Dry Docking Survey
After returning to shore, damaged ships are taken to dry docks for a complete survey. Dry docking is the simple process of removing boats from the water so workers can inspect the hull’s underside and other parts like the rudder and propellers. Dry docks can accommodate ships that weigh more than 10,000 tons if need be.
A typical dry docking survey starts by pumping all standing water out to stabilize the ship. Then, inspectors review the plans, diagrams, specifications, and other technical documents to ensure compliance with maritime standards. They also inspect the vessel’s structural integrity, machinery, and crew workmanship.
Next, they verify that all record books, operating manuals, and other instructional materials are up to date and in their assigned places. The final step of a dry docking survey is a comparison of the damaged area vs. the ship’s original blueprints, which provides a full description of the problem’s severity.
In some cases, a dry docking survey will include extra steps to inspect unique types of damage. For example, the inspectors may use ultrasonic thickness gauging to measure the thickness of steel plates and identify areas of corrosion.
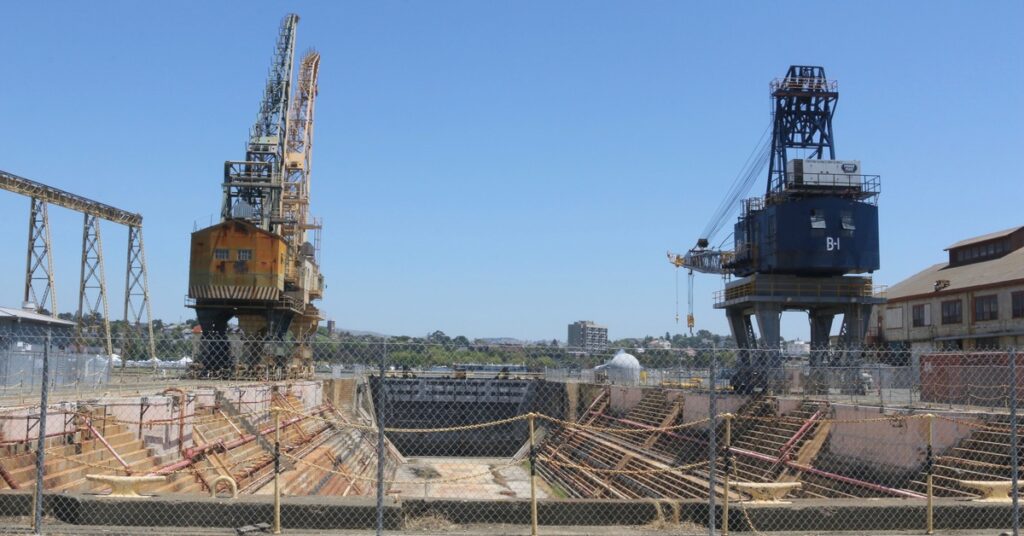
Repairs and Replacements
Once the dry dock survey is complete, it’s time to start the repairs. All renovations occur on dry docks because they allow workers to put up scaffolding and walk around the hull. Scaffolding can support four to six times its maximum load and provides a stable, level footing.
Addressing equipment damage is straightforward. The maintenance crew repairs the ship’s damaged part just like it would fix a car part. Propellers, rudders and electrical systems are among the most common culprits. Sometimes installing a replacement for the broken parts makes more financial sense.
Corrosion repairs are more complex. They must account for the ship’s essential measurements including the beam, draft, displacement, gross tonnage and waterline length. A slight structural deficiency can affect the vessel’s weight displacement and make it unsafe for overseas travel. The hull, ballast tanks, engine heat exchangers and oil tankers are most vulnerable to corrosion.
The repair team can reinforce the corroded areas with a composite material, such as epoxy resin or rust neutralizer. If the damage is too severe, they will simply cut out the corroded sections and weld new steel plates into the hull. Modern commercial ship hulls use carbon steel that’s 14-19 millimeters thick because it’s easy and inexpensive to repair.
Coating and Painting
After repairing the damaged areas and replacing the necessary parts, workers must make the ship look presentable again. They start by preparing the hull for new paint with a thorough pressure wash, degreasers and rust inhibitors. Next, they apply a protective coating of antifouling marine paint to prevent algae, barnacles and other sea life from growing.
If the ship’s deck underwent any repairs, they will also add a new coating of nonslip paint for worker safety. These paints are usually thick epoxies that bond to the surface better than normal acrylic paints. Some vessels instead opt for nanocoatings, which are ultra-thin chemical layers that improve corrosion resistance and are highly effective against saltwater.
The paint’s color isn’t just an artistic decision. Each shade serves a practical purpose, whether to keep the crew organized or improve the ship’s visibility to other vessels. For example, the hull’s underside is always painted red below the water line to indicate the ship’s cargo load, prevent marine growth or assist with emergency response.
Nondestructive Testing
Nondestructive testing is the final step in the repair process. Maintenance crews must perform these tests after making repairs to determine the integrity of their work. They might have to perform up to a dozen NDTs depending on the ship’s condition. Some common examples are moisture content evaluations, thermographic inspections, ultrasonic weld testing and gloss measurement of fresh surface coatings.
NDTs are the go-to quality assurance methods in dangerous fields such as the maritime industry. Ships must prove they can withstand extreme stress before going out to sea. Moreover, they must comply with hundreds of standards and regulations from many countries. Rigorous testing is necessary.
Shipping companies often send their newly repaired ships to facilities with special testing certifications from the International Organization for Standardization (ISO). Facilities with ISO 9001 certifications are the best at quality management, and facilities with ISO 14001 certifications specialize in environmental management.
The Fate of Irreparable Ships
When a ship is damaged beyond repair, its final resting place can be in several locations. In most cases, it’s scrapped for metal parts, electronics and other valuable components. Any salvageable items can be put to better use on another vessel. Everything else goes to a landfill or scrapyard.
If the ship has historical or sentimental value, the owners will store it on land or keep it docked in a special location. A great example is the U.S.S. Constitution, the United States’ oldest surviving naval frigate. It served in several wars in early American history and is now a public museum in the Boston Harbor.
Keeping Ships Afloat One Repair at a Time
Commercial ships wouldn’t last a decade in the ocean’s harsh environment without a thorough repair and restoration process. Many things can go wrong, and marine maintenance crews are indispensable in keeping boats and the entire industry afloat. Their jobs have only become more valuable as shipping technology advances and the demand for goods increases.
Frequently Asked Questions
When does a ship need repairs?
A ship may need repairs after suffering four types of damage — collision, structural, equipment and environmental. Vessels must also undergo inspections every 24 to 30 months regardless of their conditions so companies can make proactive repairs.
What are the key steps in the ship repair process?
The ship repair process has five main steps — the initial assessment, dry docking survey, repair and replacement, coating and painting, and nondestructive testing. These procedures are necessary to ensure structural integrity.
Where do ships go when they need repairs?
Ships that need repairs are taken to the nearest available port and removed from the water to a dry dock. Dry docks provide a safer environment and allow the maintenance crew to repair the ship’s underside.
How do shipping companies ensure their ships are safe to use?
After repairing one of its ships, the company will perform nondestructive tests — often with the help of a third-party facility — to determine its safety and compliance with industry standards. This check is essential in ensuring a vessel is safe to return to operations.
What happens to ships that are damaged beyond repair?
If a ship is too damaged to repair, it usually gets broken down for parts and metal scraps. However, an exceptional vessel or one of historical significance might be preserved on land or in a special docking area for the public to enjoy.
- The 15 Most Exciting New Ships of 2025 – January 6, 2025
- How Old Do You Have to Be to Drive a Boat? – November 12, 2024
- The Engineering Behind Ice-Class Vessels – September 20, 2024