Moving masses of goods from one end of the globe to the other sounds easy on paper. Short phrases such as “international trade” sum up an intricate process that entails the work of multiple humans and complex machinery to function. Cargo ships make up a substantial portion of the magic of moving items from the U.S. to China and vice versa, and they rely heavily on marine diesel oil (MDO) to propel them across the seas.
What is marine diesel oil, and how does it compare to other fuels used in shipping? What must industry insiders know about its effective use, and what future developments do experts have in the works to reduce emissions and make shipping cleaner and greener? Understanding the importance and function of MDO provides insight into current needs and paves the way to meeting them better. Here’s the breakdown on marine diesel oil.
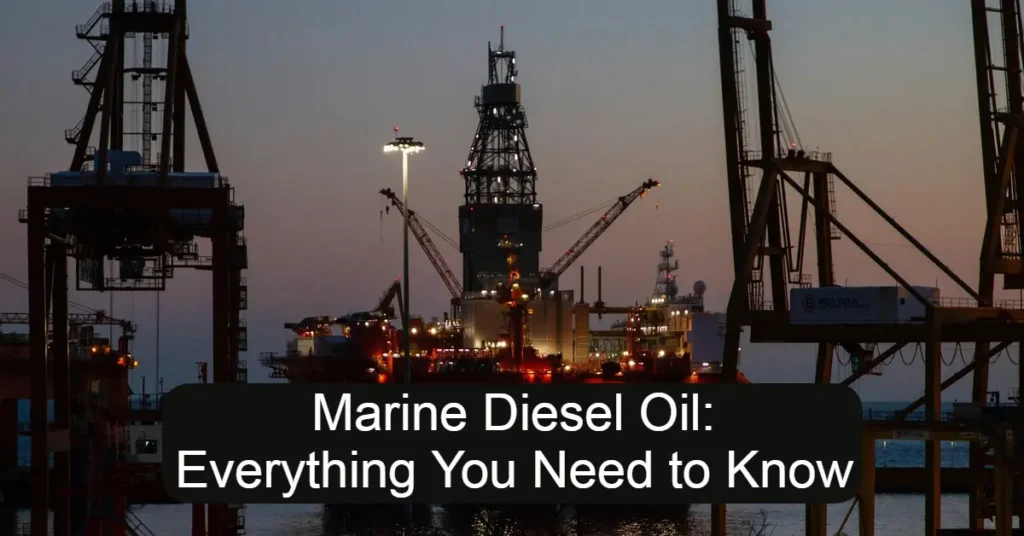
Properties and Characteristics of MDO
The average cargo ship uses the equivalent of 1,000 cars’ worth of fuel in a single day. It makes sense when you consider their massive size. Experts measure a vessel’s carrying capacity in TEUs, or 20-foot-equivalent units. Think of the size of the container on the back of your average semi-truck — then realize the largest ships hold as many as 14,000 of them.
Ships use various fuels, often abbreviated HFO, MDO and MGO. HFO stands for heavy fuel oil and is the least refined and most polluting. MGO is marine gas oil, which varies from MDO in flashpoint, density, viscosity and sulfur content.
Energy Content and Specific Gravity
MDO is significantly more dense than MGO, at 920 k/mg3, while MGO has 890 k/mg3 at 15 degrees Celsius. More viscous fuels contain more energy per volume.
Flash Point and Ignition Temperature of MDO
MGO and MDO have a minimum flashpoint of 60 degrees Celsius per IMO safety standards. IMO stands for the International Maritime Organization, the primary agency responsible for safety and security in shipping and monitoring emissions.
Flashpoint refers to the temperature at which the vapor of the heated fuel will ignite. It generally sits at 61 degrees for MDO compared to 63 to 87% for MGO. The higher the flashpoint, the safer a liquid is, making MDO potentially more hazardous.
Viscosity and Pour Point Considerations
Viscosity describes a liquid’s resistance to flow. The viscosity of MGO is lower than that of MDO. This means MDO is thicker and pours less readily.
Today, cargo ships primarily rely on HFO and MDO. International regulations demand that many vessels use MDO or MGO in designated Emissions Control Areas to reduce pollution.
Types and Grades of Marine Diesel Oil
MDO comes in various types and grades. It’s not a pure distillate, meaning it can use different blending ratios. These ratios and blends impact engine performance but also pose environmental concerns.
Distillate MDO
Distillate MDO has a lower proportion of HFOs. It has a lower viscosity and sulfur content, making it comply with environmental regulations. While the low viscosity can create problems over long distances in the ship’s main engine systems, they can run on it temporarily, as can auxiliary systems to guide vessels to shore. DMB and RMA 10 fuel classifications are examples.
Residual MDO
Residual MDO contains more HFO. Therefore, it has a higher viscosity and sulfur content. It’s used to propel ships across long distances as it creates fewer potential engine issues but creates significant environmental concerns.
Blended MDO
Recently, some companies have experimented with blends of distillate and residual MDO to maximize performance while avoiding environmental degradation. They must do so while also adhering to international standards for fuel quality and compliance. Innovations include adding biofuel blends to increase environmental sustainability.
Fuel Quality and Compliance
Bad fuel can damage ships. Furthermore, fuel that produces excess emissions when burned impacts global health — pollution knows no borders. For this reason, IMO oversees quality and compliance standards, with the MARPOL Convention responsible for setting and monitoring pollution.
International Standards and Specifications
The most widely used standard in the marine industry is the ISO 8217. The latest version of these guidelines appeared in 2017. It sets parameters for MDO quality, sulfur content, viscosity and stability. Additionally, some ports in the EU, United States, China and Hong Kong have additional regulations.
Fuel Testing and Certification
Various port authorities, coordinating with certified inspection agencies, perform fuel testing on cargo ships. Crews need to see this process as critical to protecting their equipment, not simply forcing them to comply with regulations. The right fuel blends prevent engine damage, which can have serious consequences, including supply chain disruptions and job layoffs.
For example, while biofuel is a crucial advance in improving the environmental footprint of cargo ships, it holds 10 to 15 times more water than regular diesel. More water increases microbial growth and sludge buildup, decreasing fuel economy and increasing emissions.
Storage, Handling and Treatment of Marine Diesel Oil
Marine diesel oil is a dangerous substance. Oil spills spell environmental disaster, and explosions can cause harm and death with ecological degradation. Therefore, crews must take careful considerations when storing and handling this hazardous material.
Fuel Storage Considerations
Fuel must be stored at appropriately low temperatures to prevent combustion. However, it’s a delicate balancing act. The environmental regulations that call for reduced sulfur content to minimize pollution can make MDO behave like paraffin, clumping up and causing severe trouble for engine components.
Vapors from MDO can ignite. Many ships use inerting systems, which use nitrogen to create inert gas to prevent combustion during storage. However, nitrogen also contributes to emissions during bunkering and fuel transfer.
Finally, keeping out water and other contaminants is a major concern with MDO. They can cause serious damage to engine components such as fuel injectors.
Fuel Handling Practices
Ships must often refuel when they bunker at various ports. Think about how different gasoline brands affect your car’s engine performance. The same principles apply to massive cargo vessels, but the stakes are much higher and the components more intricate. Many ships have fuel oil purifiers onboard, which remove sediment and sludge from HFO, providing purified fuel for the main engine. It does so by spinning a motor at high speeds to separate particulates.
Shipping companies often buy fuel through bunker traders, who must ensure their products meet international and local regulatory standards. Bunkering occurs as fuel-carrying vessels akin to tugboats called mini-tankers connect to the larger vessel to deliver the fuel. Bunkering occasionally occurs through road bowsers or pipelines, but not for the largest ships.
Fuel Treatment and Additives
Keeping marine diesel oil free of sediment and substances like aluminum and silicon is crucial since it can cause abrasive damage to fuel system components. Furthermore, water condensation can occur in fuel tanks thanks to temperature changes. Where there is water, microbial growth can follow.
Many companies use independent testing facilities to monitor, treat and control microbial growth in fuel oil tanks. Biocides treat microbes while dewatering programs and filter changes maintain holding tank integrity.
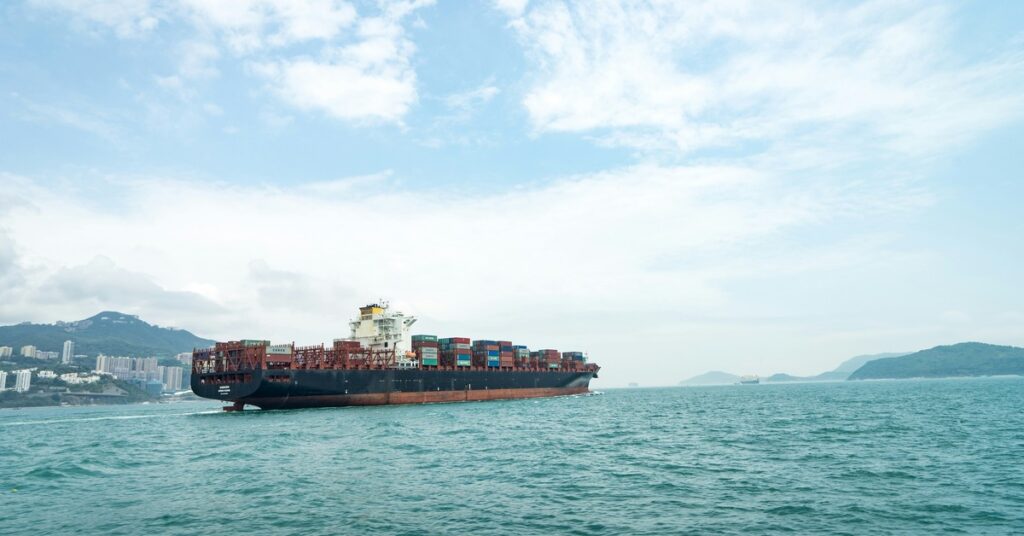
Engine Compatibility and Maintenance
Using the right oil in marine engines is crucial to protecting a vessel’s life. Additionally, crews must regularly maintain fuel systems to decrease emissions, detect early damage and rectify buildup.
Compatibility With Marine Diesel Engines
Many ships today use marine diesel engines. However, some companies have begun switching to dual-fuel motors to keep pace with environmental regulations. These are designed to run on MDO or cleaner alternatives like liquified natural gas (LFG). Crews can then balance cost-effectiveness with compliance. Although diesel remains necessary for lighting the gas, they can use a much smaller amount, producing fewer overall emissions.
Engine Maintenance Practices
Just as consumers must do with their cars, ship crews must perform routine maintenance to protect the life of their vessels. Regular monitoring for water and microbial contamination is only part of the picture. They must also maintain the filters that safeguard the various engine components.
Crews must also diagnose and address fuel-related issues. For example, deposits can foul the interior or exterior components of fuel injectors and nozzles, leading to reduced performance and eventual shutdown. Carbon deposits can likewise accumulate from burning fuel, like the soot in a standard chimney.
Environmental and Future Considerations
As the world awakens to the reality of climate change and its potential impacts, shipping companies face increasing pressure to move away from MDO and into cleaner, alternative fuel sources. Change is slow in coming, but it is necessary. Here is what’s underway, including potential benefits and roadblocks.
MDO, Air Pollution and Emissions
Sulfur oxide and nitrogen oxide are two major pollution sources from MDO. In 2023, the European Union Parliament voted to require an 80% decrease in shipping fuel’s greenhouse gas emissions by 2050. Although IMO’s goal is to cut shipping emissions by 50% by 2050, President Joe Biden recently announced pushing for a new international net-zero benchmark by the same date.
However, progress must be wise to avoid backfires. Many large ships use scrubbers to meet the stricter emissions standards established by the IMO’s 2020 sulfur cap. Unfortunately, recent research reveals that such systems often result in dumping pollutants into the water instead of the air, pushing the problem elsewhere instead of effectively solving it.
Alternative Fuels and Propulsion Technologies
Alternative fuels offer one potential solution to high ship emissions. For example, MGO fuel shares many similarities with MDO and is compatible with most marine engines. That matters because large cargo ships can take a year or more to build and last for roughly 20 years, answering the question of how to convert existing vessels. However, although it reduces emissions and improves efficiency, it is more expensive and not as widely available as MDO.
Other potential alternative fuels include biofuels, hydrogen, ethane, methane, ammonia and methanol. The primary issue with using them is a lack of infrastructure for delivery and limited supplies. Each substance has varying storage and transport requirements.
Hydrogen fuel cells and electric propulsion are other alternatives for short-distance shipping routes. However, the limited battery power range and long charging times render this technology as yet impracticable for long-distance international shipping.
Everything You Need to Know About MDO
Marine diesel oil is the blood that flows through the heart of the international shipping trade. It’s currently the best fuel source for propelling the huge cargo ships that carry the goods people rely on daily to live and work.
Although MDO is less polluting than HFO, serious concerns remain concerning its use in light of climate change. It will be fascinating to watch how the future of shipping fuel unfolds and what role MDO will play in keeping everything running by making international trade possible.
Frequently Asked Questions
Will Using MGO in an MDO Engine Cause Damage?
For the most part, no. However, crews must carefully evaluate each fuel system component to ensure compatibility and avoid damage.
Can You Mix Biofuel With MDO?
Yes, although it entails contamination risks. However, this is one method crews are using to cut emissions.
Why Haven’t More Ships Switched to Alternative Fuels to Combat Climate Change?
Updating ship engines takes time. So does installing the necessary infrastructure to transport and store alternative fuels, although many are working hard to combat climate change.
Could Ships Stop Using MDO Immediately?
At present, doing so would severely disrupt the supply chain. Instead, the focus has been to integrate new options over time in order to keep the industry running smoothly.
Where Does the Raw Material for Marine Diesel Oil Come From?
The raw material comes from crude oil, a naturally occurring, unrefined petroleum product. MDO is then blended from the distilled fractions of crude oil to reach specific viscosity and sulfur requirements.
- The 15 Most Exciting New Ships of 2025 – January 6, 2025
- How Old Do You Have to Be to Drive a Boat? – November 12, 2024
- The Engineering Behind Ice-Class Vessels – September 20, 2024