Propeller cavitation is a phenomenon that can cause significant damage to a ship’s propeller and reduce its overall efficiency.
Cavitation occurs when the pressure of a liquid drops below its vapor pressure, leading to the formation of vapor-filled cavities in the liquid.
When these cavities collapse, they create shockwaves that can erode the surface of the propeller and cause vibrations that make the ride less comfortable.
Cavitation can occur for a number of reasons, including damage to the propeller, ventilation of the water around the propeller, and the design of the propeller itself.
In order to prevent cavitation, it is important to ensure that the propeller is in good condition and that the water flow around it is smooth and uninterrupted.
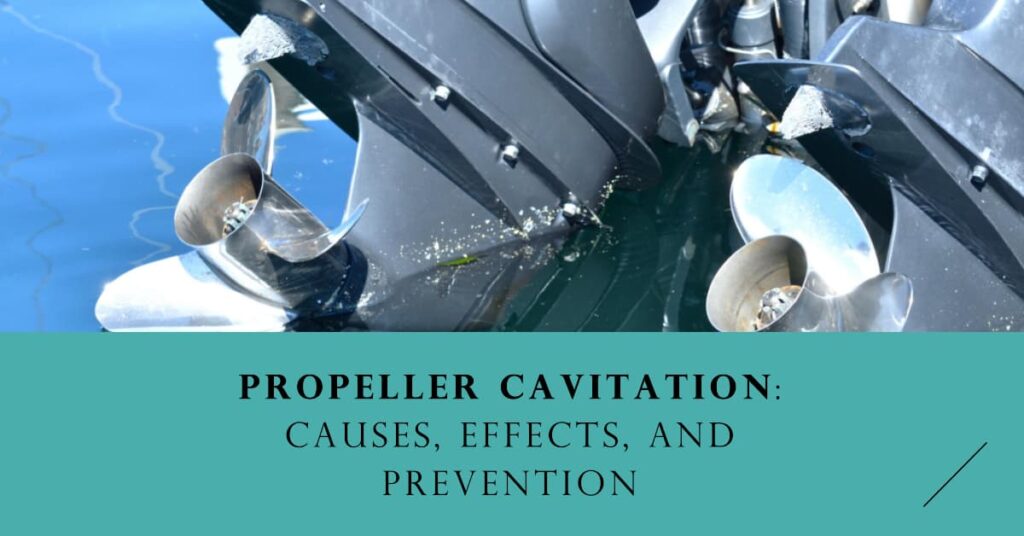
Designers can also take steps to reduce the likelihood of cavitation by using specialized materials and shapes that minimize the formation of vapor-filled cavities.
By understanding the causes and effects of cavitation, ship owners and operators can take steps to prevent damage to their propellers and ensure that their vessels operate at peak efficiency.
Understanding Cavitation
Cavitation is a phenomenon that occurs when the pressure around a propeller drops so low that water vaporizes, forming bubbles.
These bubbles can then collapse, causing damage to the propeller blades. In essence, cavitation is the formation and dissolution of vapor-filled voids, or vapor bubbles, in liquid mediums.
Cavitation can occur due to a variety of factors, including hydrodynamic factors, design factors, and operational factors.
Hydrodynamic factors include the flow pattern and flow velocity of the water, as well as the pressure waves and shock waves that are generated. Design factors include the shape and size of the propeller blades, as well as the pitch and angle of attack.
Operational factors include the speed of the boat, the depth of the water, and the load on the propeller.
When cavitation occurs, it can cause a number of negative effects. First, it can physically damage the propeller, leading to pitting and erosion of the blades.
Second, it can cause vibrations that make the ride less comfortable for passengers.
Third, it can reduce the efficiency of the propeller, as the bubbles reduce the bite of the blades on the water.
Cavitation can be classified into several types, including sheet cavitation, tip vortex cavitation, and hub vortex cavitation. Sheet cavitation occurs when the pressure drops below the vapor pressure of the water, causing a sheet of vapor to form on the blade surface.
Tip vortex cavitation occurs when the water flows around the tip of the blade, creating a vortex that can lead to the formation of bubbles. Hub vortex cavitation occurs when the water flows around the hub of the propeller, creating a similar vortex.
To prevent cavitation, it is important to ensure that the propeller is designed and operated properly. This may involve adjusting the blade shape and size, as well as the pitch and angle of attack.
It may also involve reducing the boat speed or adjusting the depth of the water in which the boat is operating.
Overall, understanding cavitation is important for anyone who operates or designs boats with propellers. By taking steps to prevent cavitation, it is possible to reduce damage to the propeller, improve passenger comfort, and increase the efficiency of the boat.
Types of Cavitation
Propeller cavitation occurs when the pressure on the surface of the propeller blade drops below the vapor pressure of the liquid, causing the formation of vapor bubbles.
These bubbles then collapse and create shock waves that can damage the propeller. There are several types of cavitation that can occur on a marine propeller as described below:
Bubble Cavitation
Bubble cavitation is the most common form of cavitation and occurs when small vapor bubbles are formed and then collapse on the surface of the propeller blade. This type of cavitation can cause pitting and erosion of the blade surface.
Vortex Cavitation
Vortex cavitation occurs when the water flow around the propeller blade creates a vortex, which in turn creates low pressure areas that can cause cavitation. This type of cavitation can cause damage to the blade surface and reduce the efficiency of the propeller.
Tip Vortex Cavitation
Tip vortex cavitation occurs when the water flow around the tip of the propeller blade creates a vortex that can cause cavitation. This type of cavitation can cause significant damage to the blade surface and reduce the efficiency of the propeller.
Sheet Cavitation
Sheet cavitation occurs when a large sheet of vapor bubbles is formed along the surface of the propeller blade. This type of cavitation can cause significant damage to the blade surface and reduce the efficiency of the propeller.
Cloud Cavitation
Cloud cavitation occurs when a large number of small vapor bubbles are formed and then collapse on the surface of the propeller blade. This type of cavitation can cause pitting and erosion of the blade surface.
Root Cavitation
Root cavitation occurs when the water flow around the root of the propeller blade creates a low pressure area that can cause cavitation. This type of cavitation can cause damage to the blade surface and reduce the efficiency of the propeller.
Face Cavitation
Face cavitation occurs when the water flow across the face of the propeller blade creates a low pressure area that can cause cavitation. This type of cavitation can cause damage to the blade surface and reduce the efficiency of the propeller.
Propeller Design and Cavitation
Propeller design is a crucial aspect of ship and boat design. It involves optimizing the propeller blades to achieve the highest possible performance, whether high efficiency or low noise levels are requested. Propeller design is especially important when it comes to preventing cavitation.
Cavitation is the formation and collapse of vapor-filled voids in liquid mediums, which can cause damage to the propeller blades and reduce efficiency. Propeller designers must take into account the potential for cavitation and design blades that minimize the likelihood of it occurring.
One important factor in propeller design is the blade shape. The trailing edge, suction side, and pressure side of the blade must be carefully designed to minimize the potential for cavitation.
Propeller diameter and pitch are also important considerations. A propeller with too large a diameter or too steep a pitch can cause cavitation, while a propeller with too small a diameter or too shallow a pitch will not be efficient.
The ideal propeller is an infinitely thin disc with an infinite number of blades, but this is not practical for real-world applications. Instead, blade element theory is used to design efficient propellers.
This theory involves dividing the blade into small sections, or elements, and analyzing the forces acting on each element. The resulting data is used to optimize the blade shape and minimize cavitation.
Other factors that can affect cavitation include the boss, or hub, of the propeller, and the use of a controllable-pitch propeller (CRP).
The boss can cause turbulence and cavitation, so it must be designed to minimize this effect. A CRP can be adjusted to optimize the angle of attack of the blades, which can reduce cavitation and improve efficiency.
Overall, propeller design is a complex process that requires careful consideration of multiple factors to minimize the potential for cavitation.
By optimizing the blade shape, diameter, and pitch, and taking into account the boss and use of a CRP, designers can create efficient and reliable propellers that minimize damage from cavitation.
Effects of Cavitation on Propellers
Cavitation is a phenomenon that can cause a range of negative effects on a ship’s propeller. When cavitation occurs, it can lead to a reduction in propelling efficiency, as well as rapid degradation of the propeller. This section will explore the various effects of cavitation on propellers.
Efficiency and Power
Cavitation can have a significant impact on the efficiency and power of a propeller. When cavitation occurs, it can cause a reduction in the propeller’s efficiency, which can lead to an increase in fuel consumption and emissions.
This reduction in efficiency can also lead to a decrease in the power that the propeller is able to generate, which can have a negative impact on the performance of the ship.
Erosion and Thrust
Cavitation can also cause erosion and thrust issues for a propeller. When cavitation occurs, it can cause erosion of the metal surface of the propeller, which can lead to pitting and corrosion. This erosion can also lead to a decrease in the thrust generated by the propeller, which can have a negative impact on the ship’s performance.
Noise and Vibration
Cavitation can cause noise and vibration issues for a ship’s propeller. When cavitation occurs, it can cause vibrations that can be felt throughout the ship. This vibration can cause noise, which can be a nuisance for crew members and passengers. It can also cause damage to the ship’s structure over time.
Resistance and Wear
Cavitation can cause resistance and wear issues for a propeller. When cavitation occurs, it can cause wear on the propeller blades, which can lead to a decrease in the propeller’s efficiency. This wear can also lead to a decrease in the lifespan of the propeller, which can be costly to replace.
Implosion and Scale Effects
Cavitation can cause implosion and scale effects for a propeller. When cavitation occurs, it can cause implosion of the microscopic bubbles that form on the propeller blades. This implosion can cause damage to the propeller blades over time.
Additionally, scale effects can occur when the size of the propeller is scaled up or down. This can cause changes in the pressure field around the propeller, which can lead to cavitation issues.
In conclusion, cavitation can have a range of negative effects on a ship’s propeller. These effects can impact efficiency, power, erosion, thrust, noise, vibration, resistance, wear, implosion, scale effects, and more.
It is important to understand the causes of cavitation and take steps to prevent it from occurring to ensure the propeller operates at maximum efficiency.
Historical Context and Key Figures
Propeller cavitation has been a topic of interest to researchers and designers since the early days of ship propulsion. In the 19th century, Robert Edmund Froude and his brother William Froude conducted experiments on propeller designs and were among the first to recognize the phenomenon of cavitation.
They observed that as the speed of the propeller increased, the pressure on the blades decreased, causing bubbles to form and collapse, leading to damage to the propeller blades.
Leonhard Euler, a Swiss mathematician, was the first to describe the basic principles of fluid flow and was instrumental in the development of the modern theory of hydrodynamics.
He provided the mathematical framework for understanding the behavior of fluids and the forces acting on bodies immersed in them.
John Isaac Thornycroft, a British naval architect, was one of the pioneers of high-speed naval architecture. He made significant contributions to the design of fast torpedo boats and developed the first practical hydrofoil.
He also conducted experiments on propeller cavitation and developed methods for predicting cavitation inception.
Sydney Walker Barnaby, a British physicist, was a leading expert on fluid dynamics and made significant contributions to the understanding of propeller cavitation.
He developed a theory for predicting the onset of cavitation and conducted experiments to verify his predictions. His work laid the foundation for modern methods of propeller design.
W.J.M. Rankine, a Scottish civil engineer, was one of the pioneers of modern engineering science. He made significant contributions to the development of the theory of fluid mechanics and was the first to describe the phenomenon of cavitation in detail.
His work provided the basis for the modern understanding of the behavior of fluids and the forces acting on bodies immersed in them.
In summary, the early pioneers of fluid mechanics, naval architecture, and engineering science made significant contributions to the understanding of propeller cavitation. Their work laid the foundation for modern methods of propeller design and continues to be relevant today.
Mathematical and Theoretical Models
Propeller cavitation is a complex phenomenon that requires a mathematical and theoretical understanding to design effective propulsion systems.
Mathematical models based on fluid dynamics principles are used to predict the onset of cavitation, its severity, and its impact on the performance of the propeller.
One of the most widely used models is the momentum theory, which assumes that the fluid flow around the propeller is inviscid and incompressible.
This model provides a simple and accurate prediction of the thrust and torque generated by the propeller. However, it does not account for the effects of cavitation on the performance of the propeller.
To incorporate the effects of cavitation, more complex models are required. One such model is the disk actuator theory, which considers the propeller as a series of disk-shaped actuators that generate thrust and torque.
This model includes the effects of cavitation and provides more accurate predictions of the performance of the propeller.
Another important aspect of cavitation is the inception of cavitation bubbles. The Bernoulli’s principle is used to predict the onset of cavitation by considering the pressure drop across the blade area. The pressure drop is related to the fluid velocity and the blade geometry, and it determines the likelihood of cavitation inception.
In addition to the mathematical models, theoretical models are also used to understand the physical mechanisms of cavitation. These models consider the flow around the propeller and the properties of the fluid, such as temperature and pressure. They also account for the effects of evaporation and boiling, which are important factors in the formation and collapse of cavitation bubbles.
Overall, the mathematical and theoretical models provide a valuable tool for understanding and predicting the performance of propellers in cavitating conditions. However, they require careful calibration and validation through experimental tests to ensure their accuracy and reliability.
Innovations and Future Trends
In recent years, there have been several innovations in propeller technology aimed at reducing underwater radiated noise (URN) and emissions. These innovations include the use of composite materials and advanced computer simulations to design more efficient propellers.
Composite materials, such as carbon fiber and fiberglass, have been increasingly used in propeller manufacturing due to their high strength-to-weight ratio and corrosion resistance. This allows for the production of lighter and more durable propellers, which can reduce fuel consumption and emissions both on ships and boats.
Advanced computer simulations have also been used to design more efficient propellers. By simulating the flow of water around the propeller, designers can optimize its shape and reduce cavitation, which can cause noise and damage to the propeller. This approach has led to the development of quieter and more efficient propellers, which can reduce URN and emissions.
In addition to these innovations, there are several future trends in propeller technology that are worth noting. One such trend is the use of permanent magnet motors, which can turn the propeller shaft from the periphery instead of the center. This can improve efficiency and reduce noise.
Another trend is the development of nozzle systems that spray compressed air over the propeller to create a macro bubble. This can reduce the possibility of cavitation, which can cause noise and damage to the propeller.
Overall, these innovations and future trends in propeller technology are aimed at reducing URN and emissions while improving efficiency and durability. As technology continues to advance, it is likely that we will see even more innovative solutions to these challenges in the years to come.
Frequently Asked Questions
What are the symptoms of propeller cavitation?
Propeller cavitation can cause several symptoms, including a decrease in thrust, increased vibrations, and increased noise. Boaters may also notice a decrease in speed or an increase in fuel consumption. In severe cases, cavitation can cause damage to the propeller blades.
How does cavitation damage propellers?
Cavitation can cause damage to propellers in several ways. When bubbles collapse near the surface of the blade, they can cause pitting and erosion. This can lead to a loss of efficiency and an increase in noise and vibration. In extreme cases, cavitation can cause chunks of material to break off the blade.
What causes cavitation burn on a propeller?
Cavitation burn is caused by the heat generated when bubbles collapse on the surface of the propeller blade. This heat can cause localized melting and damage to the blade surface, which can reduce efficiency and increase noise and vibration.
What techniques can prevent propeller cavitation?
Several techniques can be used to prevent propeller cavitation, including reducing the blade loading, increasing the blade area, and improving the blade shape. Other methods include using a nozzle system or an air-filled rubber membrane to reduce cavitation.
What is the difference between propeller cavitation and ventilation?
Propeller cavitation occurs when bubbles form and collapse near the surface of the blade, while ventilation occurs when air is drawn into the propeller blades, causing a loss of thrust. Ventilation is often caused by aeration from waves or by the boat being too close to the surface of the water.
What are some common types of propeller cavitation?
Some common types of propeller cavitation include face cavitation, tip cavitation, and vortex cavitation. Face cavitation occurs on the driving face of the propeller, while tip cavitation occurs at the tip of the blade. Vortex cavitation is caused by the formation of vortices behind the blade.
- Types of Gas Carriers as per IGC Code – April 22, 2025
- Wind-Assisted Propulsion Systems (WAPS): A Game Changer for Maritime Decarbonization – February 6, 2025
- 10 Boat Salvage Yards in California – January 25, 2025