Companies in the marine manufacturing space must have tight and effective quality control processes. Many of these businesses make high-value items that must abide by international regulations. Additionally, when people buy products made by marine manufacturers, they place significant trust in the items. What steps should an effective quality control process include?
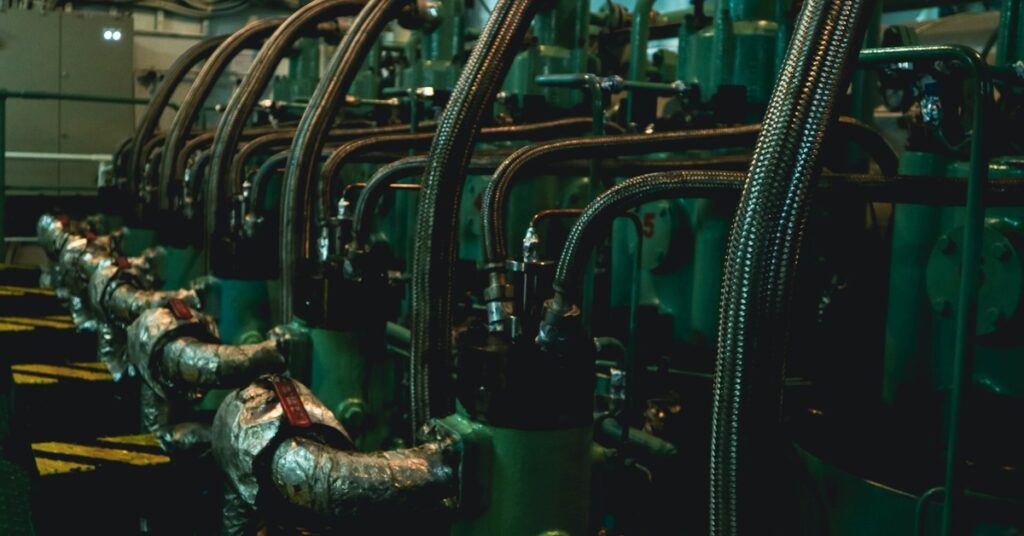
Review the Product’s Design
The quality control process must begin with engineers and other professionals verifying that an item will perform as expected in real-world conditions. After all, a flashy-looking ship may get initial interest from the audience. Still, it will receive attention for all the wrong reasons if representatives don’t catch issues in time.
One example came when a manufacturing recall impacted 3,257 boats affected by issues such as improper engine ventilation and electrical faults. Even though many of those flaws emerged decades ago, some potential purchasers have still felt wary and looked to other brands to meet their needs.
Scrutinizing a product’s design may not catch all issues in advance, but it should substantially reduce what slips through the cracks. It’s even better to involve multiple people in each review stage, increasing oversight and accountability. Participants should always check each design aspect against relevant regulations. Being careful before marine-bound products leave factories is an excellent way to prevent costly issues later.
Scrutinize the Materials and Components
Just one faulty part or flawed material could cause parts to fail quality checks. However, being proactive prevents problems by giving people more time to address possible issues before they get out of hand.
Decision-makers should start by regularly engaging with suppliers and setting minimum standards they must meet to maintain relationships. If manufacturers identify issues throughout the supply chain, they should immediately work with the relevant parties to determine what went wrong and prevent repeat occurrences.
Ongoing supplier engagement is also crucial for allowing marine manufacturers to provide accurate lead times to customers. The lead time indicates how long it takes to make and deliver products to buyers. There are three main lead time types impacting outcomes. They affect manufacturing, deliveries and order processing. Although a manufacturer’s production capacity affects lead time, so do factors outside its control, such as weather and transit route disruptions.
Examine Current Processes
A practical way to get a quality control baseline reading in manufacturing is to study individual processes to learn which aspects of them work well and which need urgent improvement. A related activity is to talk to the employees who handle those tasks daily, asking them which steps take the most time or are particularly error-prone even if people take the necessary care when performing them.
Their answers may reveal the areas to focus on to strengthen quality control. For example, molds are important parts of the manufacturing process, shaping everything from seats to hulls. However, parts can get damaged if it is too hard to remove them from the mold at the appropriate times. Fortunately, mold-release agents can address the matter. Some companies offer customized formulations, performing stringent research and testing to meet clients’ unique needs.
Workers are valuable resources for positively influencing quality control decisions. While spending most of their time on the factory floor, they gain personal experiences with production activities executives may not know as intimately.
Once leaders evaluate processes, they should strongly consider choosing key performance indicators (KPIs) to monitor and review at selected intervals. Tracking overall equipment effectiveness, downtime, defect rates and costs allows company representatives to see how things change over time. Evidence of a significant, adverse change in a short period could motivate leaders to pinpoint and fix an issue’s cause. KPIs provide snapshots of manufacturing activity and effectiveness.
Establish Best Practices for All Manufacturing Stages
Executives must also implement industry-leading practices for assembling and testing marine manufacturing products. Items such as calipers and ultrasonic imaging equipment can verify whether created parts are within specifications.
Prioritizing what happens inside a factory can influence what happens once products leave it. For example, cargo ships last 20-30 years on average, depending on use and care. However, manufacturing practices shorten products’ life spans, mainly if producers don’t spot issues before items leave factories.
Creating checklists, internal assembly manuals and other official documentation to support staff is one of the best ways to help them during their tasks. Relying on those resources will aid them in sharpening their processes and preventing issues that could cause components to fail in the quality control stage.
It is also important that maritime manufacturers publish official guides for buyers to refer to after purchase. That content can recommend how often they should perform specific maintenance tasks to keep their boats performing well.
For example, vessels that spend significant time in the water need bottom paint applied to the part that remains under the surface. The ideal frequency is usually every year or two, although the type of coating varies depending on the boat. Giving purchasers clear guidance for caring for their items will reduce the chances of unwanted outcomes caused by inadequate maintenance, for which buyers blame the manufacturer.
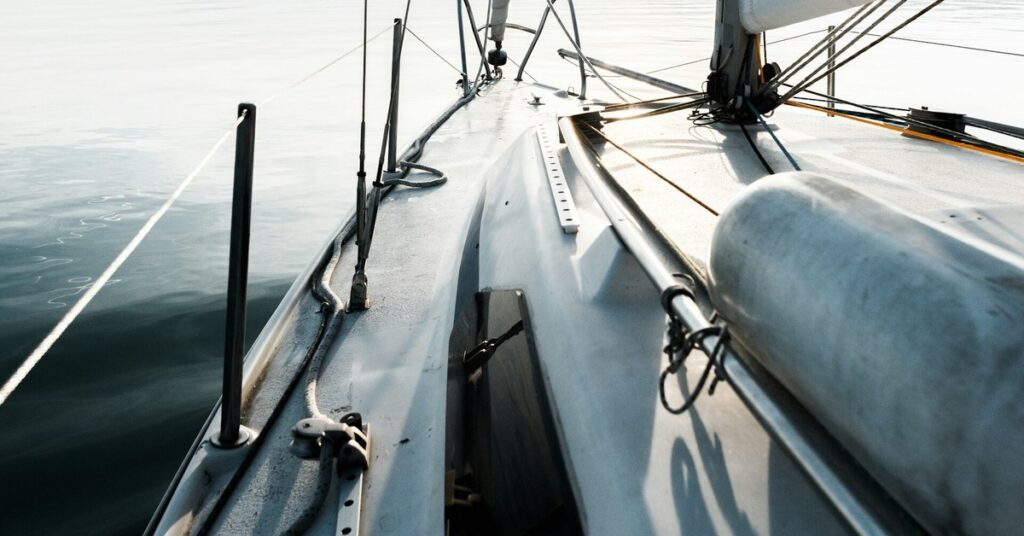
Schedule Time for Ongoing Learning Opportunities
People working in maritime manufacturing roles should grow and develop their skills. It is also best for them to engage with peers and get details about what strategies others have implemented to improve outcomes. Some of these activities can occur online, especially since many brands offer targeted, internet-based training for people at all career levels.
However, attending face-to-face events is also valuable. One example is the programming from an October 2024 boat-building conference. The content spans 10 educational tracks and more than 50 seminars. Encouraging team members to share what they learned at such gatherings is excellent for fostering knowledge-sharing, particularly benefiting those unable to attend.
Listen to Customers’ Feedback
Buyers’ comments can sometimes contain the first clues of a quality control shortcoming. That’s why giving them numerous ways to contact maritime enterprises for support is wise. When evaluating which communication channels to provide, those involved should look for the most convenient options while anticipating people’s expectations.
For example, many manufacturers will find it sufficient to offer a phone number, email address and social media channels as contact methods. However, it may be necessary to go further when catering to those buying high-end products.
Recommendations suggest luxury yacht owners should set aside 10% of the vessel’s cost to cover operational and maintenance expenses. Once someone has spent millions of dollars on their yacht, they may expect to have a dedicated contact method, such as a line that goes directly to the representative who sold it to them.
Regardless of manufacturers’ customer engagement methods, they should task workers with compiling the data and tracking relevant trends. The information could highlight potential quality control issues faster, allowing people at the affected organizations to investigate and control the matters.
Understand the Ripple Effects of Quality Control Measures
Marine manufacturing professionals never forget that any established quality control decisions could have far-reaching impacts outside factories. One time that could become apparent is during a ship’s vetting inspection. The check allows prospective charterers to verify the vessel meets industry and regulatory standards.
Additionally, tight quality control within a factory should have long-lasting reputational benefits, giving current and potential customers assurance that their chosen brand is high-quality and will provide products that perform well for years to come.
Recognize How Emerging Trends Could Change Marine Manufacturing
Marine manufacturing workers must realize their quality control procedures may evolve based on industry developments. Many customers are increasingly conscious of sustainability, which could influence future production decisions. One six-month cradle-to-grave emissions study of ships had some surprising conclusions affecting manufacturers.
For example, producers could reduce emissions by 60% by using renewable energy at shipyards. Using low-emission steel can also yield gains. However, switching to different materials may require additional or different quality control measures.
Marine Manufacturing Quality Control Is Essential
Meeting quality control standards will help marine manufacturers create or maintain solid reputations for outstanding items. The above strategies will help them set and achieve those goals.
Frequently Asked Questions
What is a lead time?
Lead time encompasses the period required to produce and deliver products to customers. Both external and internal factors can influence it and affect quality control outcomes.
What are key performance indicators?
Key performance indicators (KPIs) are selected tracked metrics that give additional information about manufacturing outcomes. They can provide leaders with better insight into costs, downtime and more.
Which factors affect a ship’s longevity?
How long a ship lasts depends on its overall usage and how well people maintain it. However, manufacturing practices can also impact life span since unaddressed quality issues may only arise once customers begin using the vessels.
Why should manufacturers include maintenance guidance for product owners?
Poor maintenance can shorten the life span of products made in marine manufacturing facilities. Such outcomes can cause customers to attribute those issues to a factory problem rather than improper maintenance. Additionally, owners may void their warranties if they do not complete specific measures on the required schedule.
How does a ship’s vetting inspection connect to quality control?
Vetting inspections occur when parties interested in chartering ships examine the vessels to ensure they align with industry standards and regulatory requirements. Thorough quality control checks during production substantially reduce the chances of uncovering issues during these checks.
- The 15 Most Exciting New Ships of 2025 – January 6, 2025
- How Old Do You Have to Be to Drive a Boat? – November 12, 2024
- The Engineering Behind Ice-Class Vessels – September 20, 2024